Turning and milling stock increases the precision and efficiency of the manufacturing process
Release time:05-07-2023
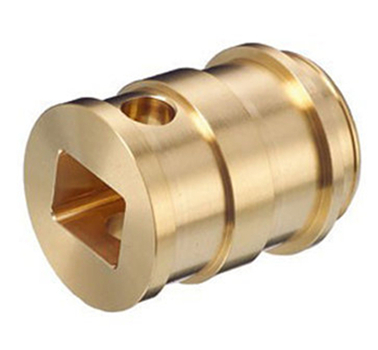
Understanding Turning and Milling Stock
The Basics of Turning Stock
Turning stock is a machining process that involves rotating a workpiece while a cutting tool traverses across its surface. The primary objective of turning is to create cylindrical components with high precision and smooth finishes. The workpiece, typically mounted on a lathe, rotates about its axis, while the cutting tool removes material to achieve the desired shape and dimensions. Turning is commonly used for creating shafts, pins, threads, and other cylindrical parts.
The Basics of Milling Stock
Milling stock, on the other hand, refers to the process of removing material from a workpiece using rotating cutting tools. Unlike turning, milling involves the movement of the cutting tool itself, while the workpiece remains stationary. The cutting tool can move along multiple axes, allowing for the creation of complex shapes, contours, and profiles. Milling is widely used in industries such as automotive, aerospace, and electronics to manufacture components like gears, brackets, and molds.
Key Differences Between Turning and Milling Stock
Machining Techniques
The fundamental difference between turning and milling lies in the machining techniques employed. Turning involves rotational motion of the workpiece, while milling involves translational motion of the cutting tool. This variance in motion fundamentally affects the way material is removed and shapes are formed.
Tooling and Workpiece Orientation
In turning, the cutting tool is rigidly mounted and moves along the workpiece's surface. The workpiece rotates about its axis, allowing for precise control over dimensions and surface finish. Conversely, milling employs various cutting tools that can move along different axes, enabling the creation of intricate features and complex geometries.
Surface Finish and Accuracy
Turning is known for its exceptional surface finish and dimensional accuracy. The continuous rotation of the workpiece enables smoother cuts, resulting in refined surfaces. Milling, while versatile, may produce slightly rougher finishes due to the intermittent cutting motion. However, modern milling techniques and advanced tooling have significantly improved surface finish capabilities.
Applications of Turning Stock
Creating Cylindrical Components
Turning stock finds extensive use in manufacturing cylindrical components, such as shafts, bushings, and connectors. The rotational movement of the workpiece, combined with precision cutting tools, allows for precise control over diameter, length, and surface finish. Turning is particularly suitable for applications that require high concentricity and tight tolerances.
Taper Turning
Taper turning is a specialized turning operation used to create tapered surfaces on workpieces. This technique is widely employed in industries like aerospace and tool manufacturing, where taper angles are crucial for proper functionality. By adjusting the tool's position relative to the rotating workpiece, precise taper angles can be achieved.
Facing Operations
Facing operations involve creating flat surfaces perpendicular to the workpiece's axis. Turning allows for efficient facing operations, ensuring the creation of smooth and precise surfaces. It is commonly used for creating flat ends on shafts, flanges, and other components that require accurate perpendicularity.
Applications of Milling Stock
Contouring and Profiling
Milling stock excels in creating complex shapes, contours, and profiles on workpieces. With the ability to move along multiple axes, milling machines can produce intricate designs with high precision. This capability makes milling ideal for manufacturing components like molds, dies, and prototypes that require intricate geometries.
Drilling and Boring
Milling machines equipped with appropriate tooling can efficiently perform drilling and boring operations. Whether it's creating holes, enlarging existing holes, or producing precise bores, milling provides excellent versatility. This capability is vital in industries like construction, automotive, and electronics, where accurate hole placement is critical.
Slotting and Keyway Cutting
Milling machines equipped with slotting or keyway cutters can precisely create slots and keyways on workpieces. These features are essential for connecting components, aligning parts, and facilitating mechanical operations. Milling's ability to accurately produce slots and keyways makes it indispensable in industries such as manufacturing, assembly, and repair.
Advantages of Turning and Milling Stock
Enhanced Precision
Turning and milling stock offer exceptional precision in manufacturing processes. Both techniques allow for tight control over dimensions, tolerances, and surface finishes. This precision ensures the creation of high-quality components that meet the desired specifications.
Efficient Material Removal
Turning and milling stock enable efficient material removal, optimizing manufacturing processes. By employing high-speed cutting tools and advanced machining strategies, manufacturers can achieve higher productivity and reduced production times. The ability to remove material quickly and accurately enhances overall efficiency.
Versatility in Design
Both turning and milling stock offer versatility in design, allowing for the creation of various geometries and features. Whether it's cylindrical components, intricate profiles, or complex contours, these machining techniques can bring diverse designs to life. This versatility enables engineers and designers to unleash their creativity and explore innovative solutions.
Choosing the Right Technique for Your Needs
Factors to Consider
When deciding between turning and milling stock, several factors should be taken into account. These include the desired component geometry, material properties, production volume, and cost considerations. Assessing these factors will help determine the most suitable machining technique for a specific application.
Material Considerations
Different materials may require specific machining techniques due to variations in their hardness, brittleness, or heat resistance. For instance, turning is generally more suitable for ductile materials like aluminum or mild steel, while milling excels in machining harder materials such as stainless steel or titanium. Understanding the material properties is crucial in selecting the appropriate technique.
Complexity of the Component
The complexity of the desired component also plays a role in technique selection. Turning is better suited for simpler geometries, while milling is ideal for intricate designs. Consider the required features, tolerances, and surface finish when deciding between the two techniques.
Where to buy turning and milling stocks?
Boyang Hardware and Plastic Products Co.,Ltd has about 20 years of proven precision in manufacturing,covers 3000 square meters.We have 30sets of CNC MACHINING CENTER,3D inspection instrument, Creative engineering team and Strict QC department.We will be your best partner.